I worked ceaselessly throughout to steadily drop the noise floor, and to remove impediments from true speed stability (in the motor, in the bearing, via mass and direct coupling), and to put the sound of materials, isolated and in combination, to work.
With the Reference Lencos I created, with regards to the plinth, a “Symphony in Wood”, tapping into the energies trapped in various but very specific solid woods to give superb atmospherics and detail, while being controlled, via my building techniques and various materials, so as to give a tonally accurate result and a great sense of realism. This was married to a symphony of carefully tested and chosen metals and plastics, to achieve, together (plinth and modified and rebuilt machine) state-of-the-art noise floors and extreme accuracy of information, timing, dynamics and bass.
Then the Reference Lenco MKIII, which started as a test-bed for the elements which go into the making of the Ultimate: 1) a new platter (had to listen to and evaluate the sound of various alloys; as well a test mass and its effect on the main bearing, etc.) and 2) the new chassis (also tested for the sound of alloys and so on) and 3) a new bearing, meant to deal with the greater stresses of the new platter, and also to lower the noise floor and improve the overall sound even further.
The basic building blocks of the Ultimate Lenco verified, to some extent, in the Reference Lenco MKIII, I turned to the plinth for the Ultimate Lenco. I started by testing the sound of very select versions of the woods I use in the Reference Lenco MKIII and MKII, which I did by building a plinth from them, and then comparing two otherwise identical Reference Lenco MKIIIs. The experiment was a success, with very audible improvements across the sonic board (greater dynamics, richness and atmospherics, bass), and so I set out to acquire volumes of the very rare necessary materials for future Ultimate Lenco commissions.
All that done, the Ultimate is built around the new platter, which is 14 1/4″ in diameter, and of a different alloy than the Reference platter to compensate for the extra mass: the aim is to increase inertia without appreciably increasing overall mass, a far more intelligent and effective method than simply building up platters vertically with enormous mass. The increase in diameter results in superior inertia, which results in another improvement of speed stability – which is ALWAYS audible across the board.
The Ultimate main bearing is designed for the Ultimate but is a component of the Reference Lenco MKIII, and is a carefully-designed mix of engineering and materials, same as every other aspect of my work. I wanted to keep these elements and so keep stress on it as low as possible, which meant achieving a total mass close to that of the Reference Platter, which is the final touch for the Reference Lenco series. So, the increase in inertia of the Ultimate platter, rather than depending on simply increasing mass vertically (simply making it heavier), with its greater stresses and wear on the main bearing, as is common with expensive belt-drives, is achieved because the platter is spinning “faster”, and so is harder to stop. This is the principle of a bullet fired from a gun, which penetrates due to speed.
How does this work? Speed is a measure of distance over time (ex. miles per hour). The circumference of a circle is simply its length, calculated via the value pi (3.1416). The practical way of measuring circumference without mathematics is to cut a piece of string, wrap it around the edge of the disc, mark where the ends meet precisely, then straighten the string and put it against a ruler. You now have a straight line which gives you the “length”, or distance, of the outer rim.
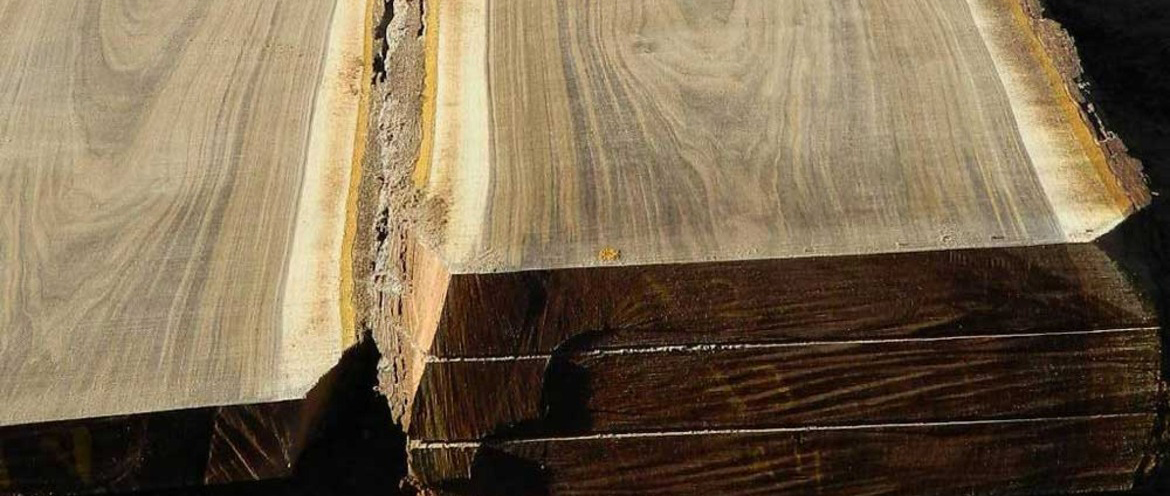
RPM means rotation per minute, so that a record player spins at 33 1/3 (33.33) rotations per minute. The “length/distance” figure for the outer rim of a 12″ platter is 37.68″; which, given 33 1/3 rpm, means 1256 inches per minute. This is its speed. The Ultimate Platter, being 14.25″ across, has a circumference of 44.745″, which is some 7″ “longer” than a regular platter, and so the rim speeds along at 1491 inches per minute, which is 235.35 inches per minute faster than a regular platter, or close to 19.6 feet per minute faster, even though the platter still spins at 33 1/3. Like a car or a bullet, the faster it goes the harder it is to stop.
Don’t forget that with a solid platter with most of its weight concentrated on the rim, the Ultimate outer rim is not only going faster, it is also heavier, 7″ of extra metal mass , making it harder to stop again, compounding the inertia where it counts, where it is going faster (like moving to a higher-calibre bullet). This should create an increase in inertia superior to that achieved by the typical vertically-increased platter at multiples of the mass of the Ultimate.
So yes, this means it has more power to overcome stylus force drag, or more simply the friction of the diamond in the groove. Is this increase of outer mass and speed – seven inches of extra material at roughly 20 feet per minute faster – audible? In fact, it is, incredibly so! This is facilitated of course by the Ultimate bearing, and by new techniques in tuning the motor, both of which remove impediments to speed stability, so allowing that greater inertia to be heard.
The platter alloy is also even more tonally accurate than the Reference Platter, which was a hoped-for outcome, which itself is a big step up from the stock platter (also due to increased speed stability due to superior machining/balance). The chassis was redesigned to accommodate the new platter, built stronger than the Reference Lenco MKIII chassis, and necessarily larger to accommodate the larger platter.
The new chassis was also tested in isolation in comparison with that of the MKIII, and found sonically superior again, once all elements had been fine-tuned to achieve an overall correct tonal balance.
As compared with the Reference Lenco MKIII + new platter, The Ultimate has superior, much more detailed and impactful bass (in fact, it is practically impossible, supernatural bass); greater palpability/sense of 3-dimensional/”thereness”; greater transient speed (though this, paradoxically, achieves a more relaxed, “real-time” live feel); greater separation of detail; greater retrieval of detail; more lingering decays; greater high frequency accuracy; and finally an absolutely rivetting, commanding presentation of the music (greater excitement and coherence, expressed as greater menace in appropriate tracks, and greater poetry in others).
It is the final word in overall performance, and in terms of emotional power and artistic intent.
Introductory price of $17,000.
A Jr., lower-priced version, will also soon be available. Contact for pricing and details.